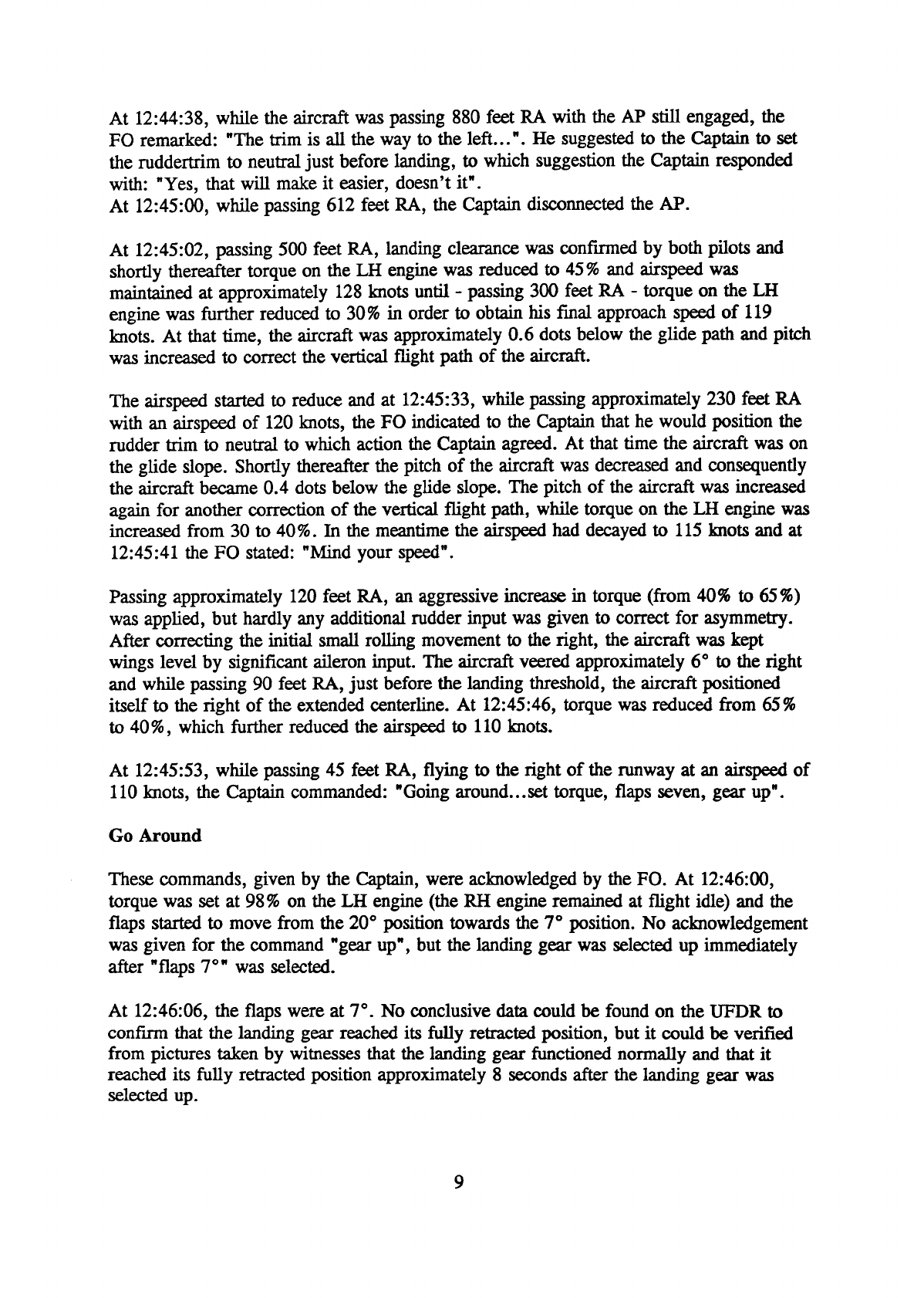
At 12
:44
:38, while the aircraft was passing 880 feet RA with the AP still engaged, th
e
F0 remarked
: "The trim is all the way to the left
. .
."
. He suggested to the Captain to se
t
the ruddertrim to neutral just before landing, to which suggestion the Captain responde
d
with
: "Yes, that will make it easier, doesn't it"
.
At 12
:45
:00, while passing 612 feet RA, the Captain disconnected the AP
.
At 12
:45
:02, passing 500 feet RA, landing clearance was confirmed by both pilots an
d
shortly thereafter torque on the
LH
engine was reduced to 45% and airspeed wa
s
maintained at approximately 128 knots until - passing 300 feet RA - torque on the
L
H
engine was further reduced to 30% in order to obtain his final approach speed of 11
9
knots
. At that time, the aircraft was approximately 0
.6 dots below the glide path and pitc
h
was increased to correct the vertical flight path of the aircraft
.
The airspeed started to reduce and at 12
:45
:33, while passing approximately 230 feet R
A
with an airspeed of 120 knots, the F0 indicated to the Captain that he would position th
e
rudder trim to neutral to which action the Captain agreed
. At that time the aircraft was o
n
the glide slope . Shortly thereafter the pitch of the aircraft was decreased and consequentl
y
the aircraft became 0 .4 dots below the glide slope
. The pitch of the aircraft was increase
d
again for another correction of the vertical flight path, while torque on the
LH
engine wa
s
increased from 30 to 40% . In the meantime the airspeed had decayed to 115 knots and a
t
12
:45
:41 the F0 stated
: "Mind your speed"
.
Passing approximately 120 feet RA, an aggressive increase in torque (from 40% to 65%
)
was applied, but hardly any additional rudder input was given to correct for asymmetry
.
After correcting the initial small rolling movement to the right, the aircraft was kep
t
wings level by significant aileron input
. The aircraft veered approximately 6° to the righ
t
and while passing 90 feet RA, just before the landing threshold, the aircraft positione
d
itself to the right of the extended centerline
. At 12
:45
:46, torque was reduced from 65
%
to 40%, which further reduced the airspeed to 110 knots
.
At 12
:45
:53, while
passing
45 feet RA,
flying
to the
right
of the
runway
at an airspeed o
f
110 knots, the Captain commanded
: "Going around
. .
.set torque, flaps seven, gear up"
.
Go Aroun
d
These commands, given by the Captain, were acknowledged by the F0
. At 12
:46
:00
,
torque was set at 98% on the
LH
engine (the
RH
engine remained at flight idle) and th
e
flaps started to move from the 20° position towards the 7° position
. No acknowledgemen
t
was given for the command "gear up", but the landing gear was selected up immediatel
y
after "flaps 7°" was selected
.
At 12
:46
:06, the flaps were at 7° . No conclusive data could be found on the
UFDR
t
o
confirm that the landing gear reached its fully retracted position, but it could be verifie
d
from pictures taken by witnesses that the landing gear functioned normally and that i
t
reached its fully retracted position approximately 8 seconds after the landing gear wa
s
selected up
.
9